Holemaking in aluminium is a crucial process that impacts the functionality, structural integrity, and performance of aluminium parts, particularly in sectors like e-mobility. To ensure efficiency and high-quality results, manufacturers need to address specific challenges such as built up edge (BUE) and excessive burrs. Here, Robert Smith, Offer Manager for Hole Making & Composites within the Solid Round Tools (SRT) Business Unit of cutting tools specialist Sandvik Coromant, provides tips and tricks for successful holemaking in aluminium. Aluminium’s desirable properties, such as low density, high strength-to-weight ratio and corrosion resistance, make it a preferred material in several applications including e-mobility. However, machining aluminium is not without challenges, one such challenge is holemaking. Accurate holemaking is as important to ensuring the proper assembly, functionality, and durability of aluminium parts. For instance, in e-mobility, precise holes enable the secure attachment of battery racks, electric motor housings and connectors and help to ensure optimal electrical conductivity and mechanical stability. Creating precise and reliable holes in aluminium presents unique challenges — mainly related to process security, BUE and excessive burrs. BUE occurs when the workpiece material softens during drilling, causing it to stick to the drill and resulting in poor surface finish and potential tool wear. Excessive burrs are unwanted rough edges that form around the drilled hole and affect the final product’s quality and functionality. Identifying these challenges is the first step toward implementing effective holemaking strategies. Minimising BUE, reducing burrs To minimise BUE during aluminium hole making, it is crucial to choose the right cutting tools and geometries. Tools with specific designs combined with dedicated coatings can reduce BUE. Selecting the appropriate drill grade and coating is also essential. Sandvik Coromant offers advanced solutions like diamond-like carbon (DLC) coatings, which preserve the sharp cutting edge required for aluminium holemaking. Reducing burrs is another critical aspect of holemaking. Employing high feed rates and utilising dedicated tool designs can help minimise burr formation. Understanding the characteristics of different aluminium alloys is crucial for successful holemaking — aluminium alloys with higher silicon content, for instance, exhibit improved strength, hardness and thermal stability. Typically, when a new automotive production line is being developed, it involves a turnkey approach. This ensures the production line is designed for purpose and has been engineered to meet specific targets, such as producing 1000 parts per shift. Once everything is set up on the factory floor, it can become challenging to make significant adjustments or tweaks later in the production process. That’s why Sandvik Coromant often gets involved with customers at the early stages of a project, working collaboration with the machine tool builder to ensure the cutting tool is suitable for not only the machine, but for the wider production line. While automotive manufacturers are already knowledgeable in their respective domains, it is valuable to introduce new concepts from cutting tool experts. Such concepts include indexable milling, a machining process using replaceable cutting inserts for milling operations, or innovative technologies like Sandvik Coromant’s new grade, hard carbon (DLC) that offers superior performance compared to true diamond coatings that are much thicker and can lead to reducing the sharpness of the cutting edge. Optimised cutting data The cutting speed, feed rate and tool geometry directly impact the efficiency and quality of aluminium holemaking. These parameters should be adjusted based on the specific application, material properties and desired outcome. Collaboration with tool manufacturers to leverage their expertise can assist in determining the most suitable parameters for efficient and high-quality holemaking. To this end, Sandvik Coromant offers a range of optimised solutions for aluminium holemaking, including the CoroDrill® 860-NM. CoroDrill® 860-NM is specifically designed for machining aluminium, offering exceptional design features and performance advantages. With a diameter range of 3.0–20.0 mm and a drill depth of 3–8 times the diameter, it provides versatility for various applications. The tool features internal coolant for efficient chip evacuation and improved tool life. Meanwhile, CoroTap® 100 & 400-N is a optimised and efficient product line designed for high performance in cutting and form tapping ISO-N applications. Of these, CoroTap® 100 is designed with a straight flute and a durable coating, making it ideal for high productivity and process security in blind and through hole applications. Its efficient cutting performance ensures reliable results. CoroTap® 400 is an optimised form tapping tool available in HSS-E and Solid Carbide substrates. It enables efficient and precise thread forming. Both CoroTap® 100 and 400 deliver increased productivity and process security, making them widely used in the automotive industry for aluminium applications. Efficient and high-quality holemaking in aluminium is vital for the successful production of aluminium parts in sectors like e-mobility. By understanding the challenges, implementing the right strategies, and utilising advanced tools and coatings, manufacturers can optimise productivity, meet industry requirements, and maintain a competitive edge in the market. To learn more about Sandvik Coromant’s tooling solutions for machining aluminium, visit its website. |
How to achieve better holemaking in aluminium
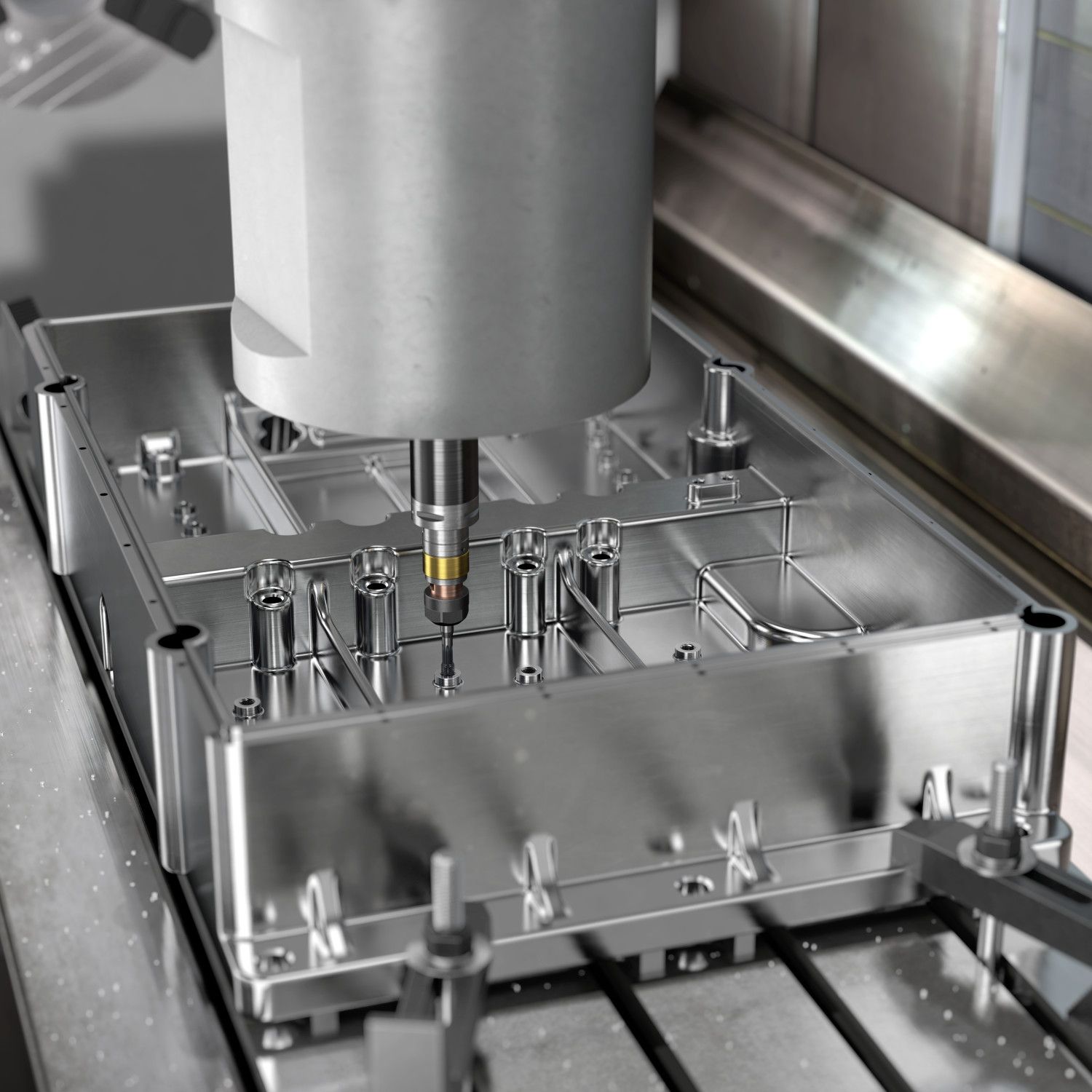